0 引言
目前工業(yè)窯爐中常用的煙氣脫硫方法有濕法、半干法、干法等化學(xué)脫除方法,其中石灰石-石膏濕法煙氣脫硫技術(shù)因技術(shù)成熟、脫硫效率高、煤種適用性強等優(yōu)勢而被廣泛應(yīng)用,特別是在燃煤發(fā)電廠。但在實際運行過程中,煙氣中氯化物、顆粒物、重金屬等污染物會不斷地富集在漿液中,易引起設(shè)備管道腐蝕、脫硫效率降低、破壞脫硫系統(tǒng)物質(zhì)平衡等問題。因此每隔一定時間就必須排出一定量脫硫廢水。由于此部分廢水具有高懸浮物、高含鹽量及重金屬種類多等水質(zhì)特性,處理難度極大。
2015年4月國家出臺《水污染行動防治計劃》(《水十條》),對火電廠工業(yè)廢水排放提出了新要求,倒逼火電廠進行全廠廢水零排放改造。2017年發(fā)布的《火電廠污染防治可行性技術(shù)指南》同樣提出要實現(xiàn)廢水近零排放的關(guān)鍵是實現(xiàn)脫硫廢水的零排放。目前深能合和電力(河源)有限公司、佛山市三水恒益火力發(fā)電廠有限公司、浙江浙能長興發(fā)電有限公司、山西大唐國際臨汾熱電有限責(zé)任公司已完成脫硫廢水零排放工程實施,它們均以多效蒸發(fā)、機械蒸汽再壓縮蒸發(fā)、膜處理技術(shù)和煙道蒸發(fā)為主要處理工藝。然而以上示范項目存在投運期短、經(jīng)濟性差、系統(tǒng)穩(wěn)定性差等問題。
本文在深入分析脫硫廢水水質(zhì)特性的基礎(chǔ)上,提出了一種低溫余熱閃蒸蒸發(fā)脫硫廢水技術(shù),并在300MW機組處理15m3/h脫硫廢水工程中進行了工程示范,目前系統(tǒng)運行穩(wěn)定,凈水回用率高,取得了很好的效果。
1 脫硫廢水特點及處理現(xiàn)狀
以山西某電廠煙氣濕法脫硫水力旋流器出口廢水為例,廢水水質(zhì)數(shù)據(jù)(設(shè)計值)見表1。由表1可知,該廠脫硫廢水懸浮物含量高(主要成分為石膏、灰分等);鈣離子、鎂離子、硫酸根離子質(zhì)量濃度高,易結(jié)垢;pH值低,呈酸性,氯離子濃度高,易引起設(shè)備及管道腐蝕;有一定的汞、鎘、鉻等重金屬;水質(zhì)參數(shù)波動大,組分復(fù)雜。
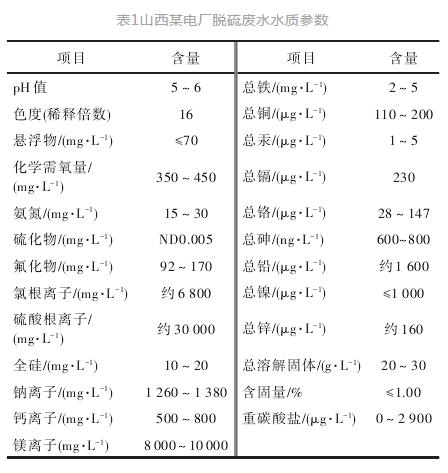
目前脫硫廢水主要通過“中和—絮凝—沉淀”三聯(lián)箱方式進行處理?;赜盟猛緩街饕懈苫艺{(diào)濕、灰場噴灑或灰渣冷卻。脫硫廢水替代在除灰、除渣系統(tǒng)調(diào)濕用水,具有系統(tǒng)改造成本低、結(jié)構(gòu)簡單、操作簡單等優(yōu)勢,但除灰、除渣系統(tǒng)所用水量遠遠小于脫硫廢水產(chǎn)生量,脫硫廢水無法得到充分利用。此外,因傳統(tǒng)預(yù)處理后的廢水中仍含有大量的氯離子,pH值低,易于對除灰、除渣系統(tǒng)管路造成腐蝕、堵塞。
2 低溫余熱閃蒸蒸發(fā)脫硫廢水零排放系統(tǒng)
2.1 低溫多效蒸發(fā)技術(shù)原理
本脫硫廢水零排放技術(shù)原理有2個突出方面,具體如下。
?。?)低溫余熱閃蒸利用原理。
本文技術(shù)根據(jù)水溶液沸點隨壓力降低而降低的原理,實現(xiàn)脫硫廢水的梯級多效蒸發(fā)濃縮。一方面,利用除塵器出口低塵低溫?zé)煔鉄崃浚⑼ㄟ^真空泵建立煙道換熱器系統(tǒng)負壓,使得換熱器中產(chǎn)生低于100℃的低溫沸騰蒸汽,作為多效蒸發(fā)系統(tǒng)的外部熱源,實現(xiàn)了煙氣廢熱的高效利用;另一方面,通過真空泵建立多效蒸發(fā)系統(tǒng)負壓,根據(jù)脫硫廢水不同壓力下對應(yīng)的沸點蒸發(fā)溫度,使得脫硫廢水在分離器負壓的作用下閃蒸成蒸汽,實現(xiàn)外部熱源熱量從Ⅰ效到Ⅲ效的梯級利用。
?。?)加熱器高效防垢原理。
采用控制流速強制循環(huán)技術(shù)、催化磁化及結(jié)晶防垢技術(shù)??刂茝娭蒲h(huán)流速,提高傳質(zhì)流動,降低了管壁結(jié)垢風(fēng)險。通過廢水磁化處理,使得處在成核條件附近無序熱運動的結(jié)垢無機鹽離子對獲得能量,被迫調(diào)整彼此碰撞方位,形成均勻成核條件,因此產(chǎn)生大量小直徑球狀微晶膠體懸浮物,破壞了硬垢形成條件。在特定位置采用特殊材料,會產(chǎn)生特定電解電流,對水起到催化作用,吸收離子,增大瞬間過飽和度,產(chǎn)生大量可逆微晶體,使得廢水飽和度大大降低,消除了生成硬垢的條件。利用晶種防垢原理,通過控制原廢水本身的石膏晶體濃度,濃縮過程中廢水中鈣離子、鎂離子、硫酸根離子等二價鹽離子優(yōu)先凝聚在固體石膏晶核上,從而減輕加熱器結(jié)垢風(fēng)險。
2.2 工藝流程
低溫余熱閃蒸蒸發(fā)技術(shù)應(yīng)用在石灰石-石膏濕法脫硫廢水零排放上的工藝流程示意如圖1所示。整個工藝主要由廢水儲存及輸送系統(tǒng)、煙道換熱器系統(tǒng)、多效閃蒸蒸發(fā)系統(tǒng)、冷卻系統(tǒng)、濃液處理系統(tǒng)、排空系統(tǒng)等6個系統(tǒng)組成。在除塵器出口至引風(fēng)機入口煙道上加裝煙道換熱器,利用除塵器出口132℃煙氣的熱量在Ⅰ效真空泵作用下將換熱器內(nèi)介質(zhì)(除鹽水)加熱成低于100℃的低溫蒸汽,并將蒸汽(熱源)送至Ⅰ效蒸發(fā)系統(tǒng)對廢水進行蒸發(fā)濃縮,蒸汽冷凝后收集在Ⅰ效冷凝罐中,再通過加濕水泵重新送到煙道換熱器。此部分為蒸發(fā)系統(tǒng)的低溫余熱獲取環(huán)節(jié)。
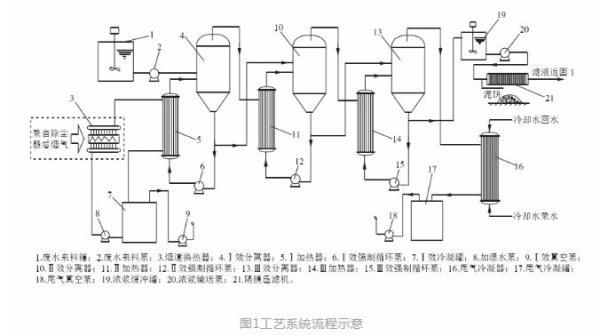
來自水力旋流器出口脫硫廢水送至廢水來料箱,經(jīng)廢水來料泵送至多效蒸發(fā)系統(tǒng)加熱濃縮。在尾氣真空泵作用下,Ⅰ效分離器中廢水在Ⅰ效加熱器管程中均勻流動,并與Ⅰ效加熱器殼程中的蒸汽進行換熱,被加熱后的廢水再進入Ⅰ效分離器完成汽、液分離,并利用Ⅰ效強制循環(huán)泵進行強制循環(huán)蒸發(fā)濃縮物料,在Ⅰ效蒸發(fā)系統(tǒng)內(nèi)經(jīng)多次循環(huán)后,完成初步濃縮的料液通過平衡管在液位壓差的作用下進入Ⅱ效分離器,同時Ⅰ效分離器產(chǎn)生的二次蒸汽進入Ⅱ效加熱器,作為Ⅱ效蒸發(fā)系統(tǒng)的熱源。以此類推,廢水不斷地濃縮結(jié)晶,凈水不斷地蒸發(fā)冷凝。***終,Ⅲ效分離器出口的二次蒸汽在尾氣冷凝器內(nèi)利用循環(huán)冷卻水將蒸汽冷凝成凝結(jié)水,收集在尾氣冷凝罐中。Ⅲ效蒸發(fā)系統(tǒng)中漿液質(zhì)量濃度被濃縮設(shè)計值大于1300kg/m³時,開啟出料閥門,利用Ⅲ效強制循環(huán)泵出口壓頭,將濃漿液送至濃液緩沖罐中儲存。此時各效因出料而產(chǎn)生液位降低,廢水在廢水來料泵和物料連通管的作用下自行補充各效分離器、加熱器內(nèi)的物料,各效物料的補充速度由進料電動閥控制,從而達到控制各效液位的目的。
濃漿液通過濃漿輸送泵送至固液分離裝置,結(jié)晶體和飽和母液經(jīng)分離后,固體被送去石膏庫,飽和母液回送至廢水來料箱,進而隨廢水重新進入多效蒸發(fā)系統(tǒng)進行濃縮結(jié)晶。上述低溫余熱閃蒸蒸發(fā)技術(shù)不同于膜法濃縮,不需要預(yù)處理,系統(tǒng)更為簡單可靠、操作更為簡便;
系統(tǒng)熱源取自除塵器出口煙氣余熱,系統(tǒng)運行成本更低;整個多效蒸發(fā)系統(tǒng)采用外熱式強制蒸發(fā)工藝,極大地降低了系統(tǒng)管道、設(shè)備結(jié)垢的可能性。
2.3 工程示范技術(shù)參數(shù)
根據(jù)山西某300MW機組煙氣條件及脫硫廢水水質(zhì)參數(shù),采用煙氣低溫余熱閃蒸蒸發(fā)脫硫廢水零排放技術(shù),投資建成了處理水量為15m3/h的脫硫廢水零排放示范工程。該工程主要工藝設(shè)備技術(shù)參數(shù)見表2。
3 應(yīng)用示范結(jié)果分析
3.1 技術(shù)經(jīng)濟性分析
按照整個系統(tǒng)試運行期間數(shù)據(jù)統(tǒng)計,該廢水零排放系統(tǒng)的直接運行成本主要包括動力消耗、除鹽水消耗和工藝水消耗量3部分。動力消耗折算至處理水量為37.67(kW·h)/m³,電價按照0.50元/(kW·h)估算,折合約18.83元/m³。除鹽水消耗量0.1t/h,除鹽水費用按照15.00元/t,折合約0.10元/m³。工藝水消耗量約為2.1m³/h,工藝水費用按照3.50元/t,折合約0.49元/m³。因此,若不考慮人員成本、設(shè)備折舊費用等,本脫硫廢水零排放系統(tǒng)總的直接運行成本約為19.42元/m³。深能合和電力(河源)有限公司采用“預(yù)處理+蒸發(fā)結(jié)晶+分鹽”技術(shù),實際零排放運行費用為70~80元/m³,本技術(shù)運行費用為19.42元/m³,遠低于上述電廠技術(shù)。
3.2 試運行結(jié)果分析
3.2.1 處理能力分析
本脫硫廢水深度處理工程項目于2019年6月26日開始并進行168h試運行,因#2機組煙氣換熱器未安裝,故系統(tǒng)處理能力設(shè)計值按照50%進行測算。數(shù)據(jù)記錄見表3。由表3可以看出,項目168h試運行期間,累計處理廢水量為681t,凝結(jié)水回收水量為632t,平均回收水率為92.8%。因機組負荷不同,除塵器出口。
表2 主要工藝設(shè)備選型
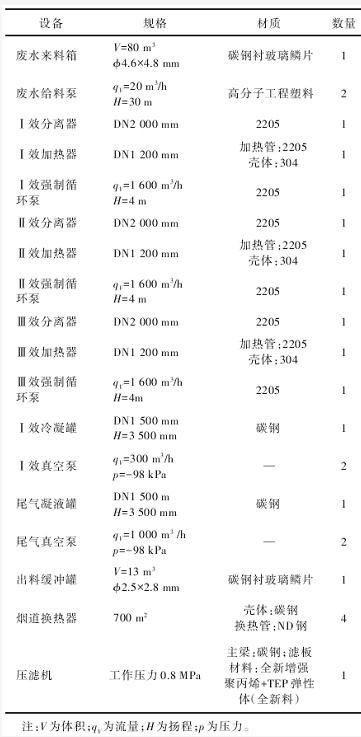
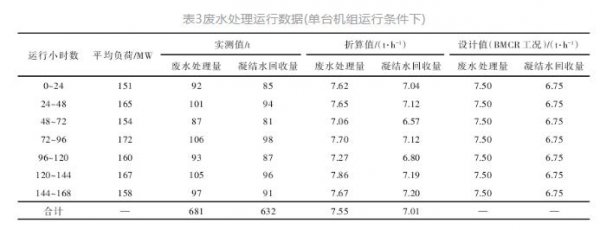
煙氣量及溫度均低于設(shè)計值。故通過負荷折算至鍋爐***大連續(xù)蒸發(fā)量(BMCR)工況下的脫硫廢水處理量平均值為7.55t/h,凝結(jié)水回收量平均值為7.01t/h,達到了設(shè)計處理能力。3.2.2出水水質(zhì)分析
試運行期間對廢水來料箱中廢水原水取樣(FS)和凝結(jié)水泵出口凝結(jié)水取樣(NS),檢測數(shù)據(jù)結(jié)果見表4。
定義去除率S=(FSi-NSi)/FSi×100%,
式中:FSi為表4中脫硫廢水原水中第i個檢測指標(biāo)測定值;NSi表示表4中凝結(jié)水中第i個檢測指標(biāo)測定值;i=2~14。
脫硫廢水處理前后,不同類檢測指標(biāo)去除率如圖2所示。從圖中可以看出,除氨氮外,脫硫廢水中其他指標(biāo)去除率均高于96%(余氯除外)。說明本技術(shù)對低沸點物質(zhì)(氨氮)的去除能力比較差。氨氮主要來源于煙氣脫硝過程中過量逃逸的氨氣,被濕法脫硫系統(tǒng)吸收后進入脫硫廢水中。
GB/T19923—2005《城市污水再生利用工業(yè)用水水質(zhì)》中鍋爐補給水水質(zhì)標(biāo)準見表5。對照表4中凝結(jié)水測定值,除氨氮指標(biāo)外,主要指標(biāo)基本達到了鍋爐補給水水質(zhì)標(biāo)準,但需進一步去除氨氮等,方可作為鍋爐補給水。此外,凝結(jié)水中氯離子、鈣、鎂、硫酸根離子質(zhì)量濃度遠小于原脫硫廢水,故此凝結(jié)水可直接作為脫硫工藝補水。
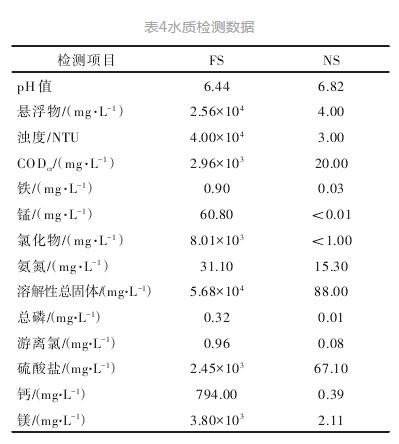
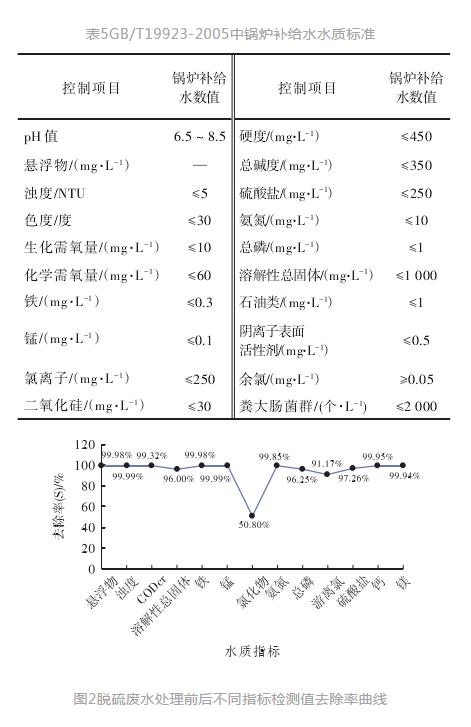
3.2.3 防結(jié)垢分析
從脫硫廢水水質(zhì)參數(shù)中可以看出,廢水中鈣離子、鎂離子、硫酸根離子等二價離子較多,水質(zhì)硬度較高,系統(tǒng)容易結(jié)垢。采用外熱式強制循環(huán)蒸發(fā),通過強制循環(huán)泵的動力,使得廢水以較高(通常大于1m/s)流速循環(huán)流動,提高了各效加熱器的換熱效率,同時降低了系統(tǒng)管道結(jié)垢的風(fēng)險。
整個系統(tǒng)連續(xù)運行40d后,停機查看系統(tǒng)結(jié)垢情況,發(fā)現(xiàn)Ⅰ效、Ⅱ效系統(tǒng)管道無結(jié)垢,Ⅲ效分離器局部有輕微結(jié)垢,高壓水沖洗后,污垢脫落。取出結(jié)垢物分析,結(jié)垢物主要為鹽類,易溶于水。3.3長期結(jié)果分析截至目前,系統(tǒng)已穩(wěn)定運行近9個月,系統(tǒng)處理穩(wěn)定,凝結(jié)水水質(zhì)指標(biāo)穩(wěn)定,***近一次停機檢查,未發(fā)現(xiàn)設(shè)備結(jié)垢。日常凝結(jié)水主要化驗電導(dǎo)率、pH值、濁度、硅、鐵離子、硫酸根及氯離子等水質(zhì)指標(biāo)。2020年3月的部分日?;灁?shù)據(jù)見表6。
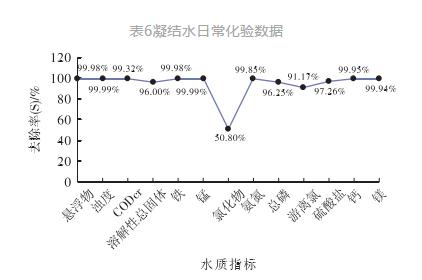
4 結(jié)束語
本技術(shù)方案利用除塵器出口低溫?zé)嵩醇柏搲洪W蒸原理,通過廢水輸送統(tǒng)、煙氣換熱器系統(tǒng)、多效蒸發(fā)系統(tǒng)、濃漿壓濾結(jié)晶系統(tǒng)和排空系統(tǒng)等六大系統(tǒng),構(gòu)建成了煙氣低溫余熱閃蒸蒸發(fā)脫硫廢水零排放工藝,并完成了15m³/h脫硫廢水零排放工業(yè)化示范。運行結(jié)果表明:系統(tǒng)運行穩(wěn)定,處理能力達到了設(shè)計要求,且運行成本低,處理每立方米脫硫廢水直接成本僅約為19.42元。
不需要預(yù)處理,利用廢水中石膏作為晶種,結(jié)合末端的壓濾結(jié)晶技術(shù),實現(xiàn)了脫硫廢水中鹽的濃縮自結(jié)晶分離。
多效蒸發(fā)單元采用了外熱式強制循環(huán)蒸發(fā)方式,能夠保證在濃縮過程中脫硫廢水循環(huán)流動,降低了系統(tǒng)結(jié)垢風(fēng)險。
多效蒸發(fā)系統(tǒng)凝結(jié)水提取率高,高達92.8%以上,凝結(jié)水進一步處理后可作為鍋爐補給水或者直接作為脫硫工藝補水。